The Essential Role of Plastic Injection Mould Makers in Modern Manufacturing
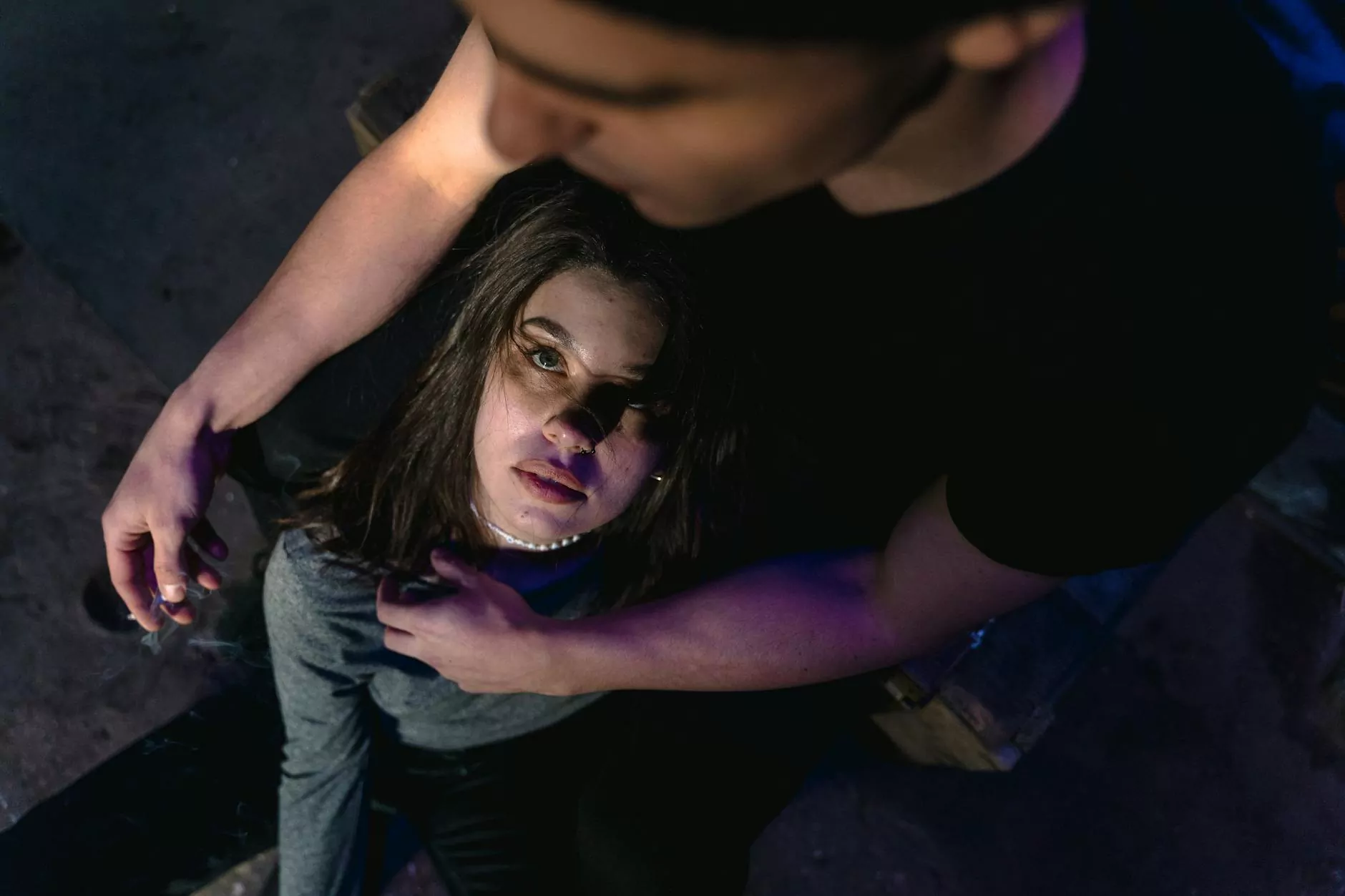
In the realm of modern manufacturing, plastic injection mould makers play a pivotal role. They are the backbone of industries that rely heavily on plastic components, from automotive to consumer goods. When it comes to efficient production and high-quality finishes, choosing the right mould maker is critical. This article will provide an in-depth exploration of the plastic injection mould-making process, the significant benefits it brings, and why collaborating with experienced professionals like Hanking Mould is vital for your production needs.
Understanding Plastic Injection Moulding
Plastic injection moulding is a manufacturing process where molten plastic is injected into a mould cavity, where it cools and solidifies into the desired shape. This method is lauded for its efficiency and ability to produce high volumes of consistent and accurate parts. Here are the key steps involved in the process:
- Design and Prototyping: The journey starts with a detailed design of the mould. Advanced software programs help create digital prototypes that streamline this phase.
- Mould Creation: High precision is required in this phase, as the moulds need to be meticulously crafted from robust materials such as steel or aluminum.
- Injection Process: Once the mould is ready, the chosen plastic resin is heated until it becomes liquid and then injected into the mould cavity under high pressure.
- Cooling and Finishing: After the plastic has cooled, the mould is opened to extract the finished product, which may then undergo additional finishing processes.
Why Choose Expert Plastic Injection Mould Makers?
When it comes to sourcing your plastic components, partnering with professional plastic injection mould makers like Hanking Mould is paramount. Here are several reasons why:
1. Quality Assurance
Professionals bring a wealth of experience and rigorous quality control standards to the table. Their expertise ensures that each mould produced meets stringent specifications, resulting in consistently high-quality parts.
2. Cost-Effectiveness
While initially, hiring proficient mould makers may seem like an unnecessary expense, it proves to be a cost-effective choice in the long run. High-quality moulds reduce production errors, ensuring less waste and quicker turnaround times.
3. Technical Expertise
Experienced manufacturers not only bring technical skills but also innovative solutions to complex challenges. Their knowledge of material properties and processing conditions enables them to suggest the best materials for your needs.
4. Customization
Every project is unique, and professional mould makers understand the need for customization. They work closely with clients to ensure the final product matches their precise specifications.
5. Advanced Technology
Top-tier plastic injection mould makers utilize the latest technologies, from CNC machining to 3D printing. This technological edge enhances precision and efficiency across the board.
Types of Plastic Injection Moulds
Understanding the different types of plastic injection moulds can help you make informed decisions for your projects. Here’s a brief overview:
- Single Cavity Moulds: Designed to create one part per cycle, these moulds are optimal for low-volume production.
- Multi Cavity Moulds: These moulds can produce multiple parts simultaneously, significantly enhancing productivity for high-volume runs.
- Stack Moulds: Stack moulds allow for the production of multiple layers of parts at once, making them a good choice for specialized applications.
- Family Moulds: Family moulds produce different but related components in the same cycle, an efficient solution for varied product lines.
The Advantages of Plastic Injection Moulding
The process of plastic injection moulding has several notable advantages that make it the preferred choice for manufacturers worldwide:
1. High Efficiency
Once the initial setup is complete, the production rate is rapid, making it highly efficient for mass production.
2. Design Flexibility
Advanced mould-making techniques allow for intricate designs that might be difficult or impossible with other methods.
3. Minimal Waste
The precision of the injection moulding process minimizes excess material, making it an environmentally friendly option as well.
4. Robust Final Products
Products created through injection moulding are known for their durability and strength, making them suitable for various demanding applications.
How to Choose the Right Plastic Injection Mould Maker
1. Experience and Expertise
Look for mould makers with a proven track record in the industry. Examine their portfolio to understand their capabilities and past projects.
2. Technological Capabilities
The use of modern technology can greatly influence the quality and efficiency of production. Ensure the mould maker you choose employs up-to-date machinery and techniques.
3. Customer Support
Strong customer support is vital. Your mould maker should be responsive and willing to work with you throughout the process, addressing any concerns or changes that may arise.
4. Quality Certifications
Look for ISO-certified mould makers. Certifications indicate compliance with international quality standards, ensuring reliability and consistency.
5. Cost and Flexibility of Services
While pricing is important, it should not be the sole factor in your decision. Evaluate the overall value and flexibility of services offered.
Conclusion: The Future of Plastic Injection Moulding
As industries continue to evolve, the demand for plastic injection mould makers will only increase. With advancements in materials and manufacturing technologies, the possibilities for innovation are limitless. Collaborating with professional mould makers such as Hanking Mould ensures that your manufacturing process remains at the forefront of efficiency, quality, and innovation.
By understanding the intricacies of the mould-making process and the benefits that come from choosing expert manufacturers, businesses can enhance production capabilities, reduce costs, and maintain a competitive edge. Embrace the future of manufacturing with confidence—partnering with the right plastic injection mould maker is the first step towards success.